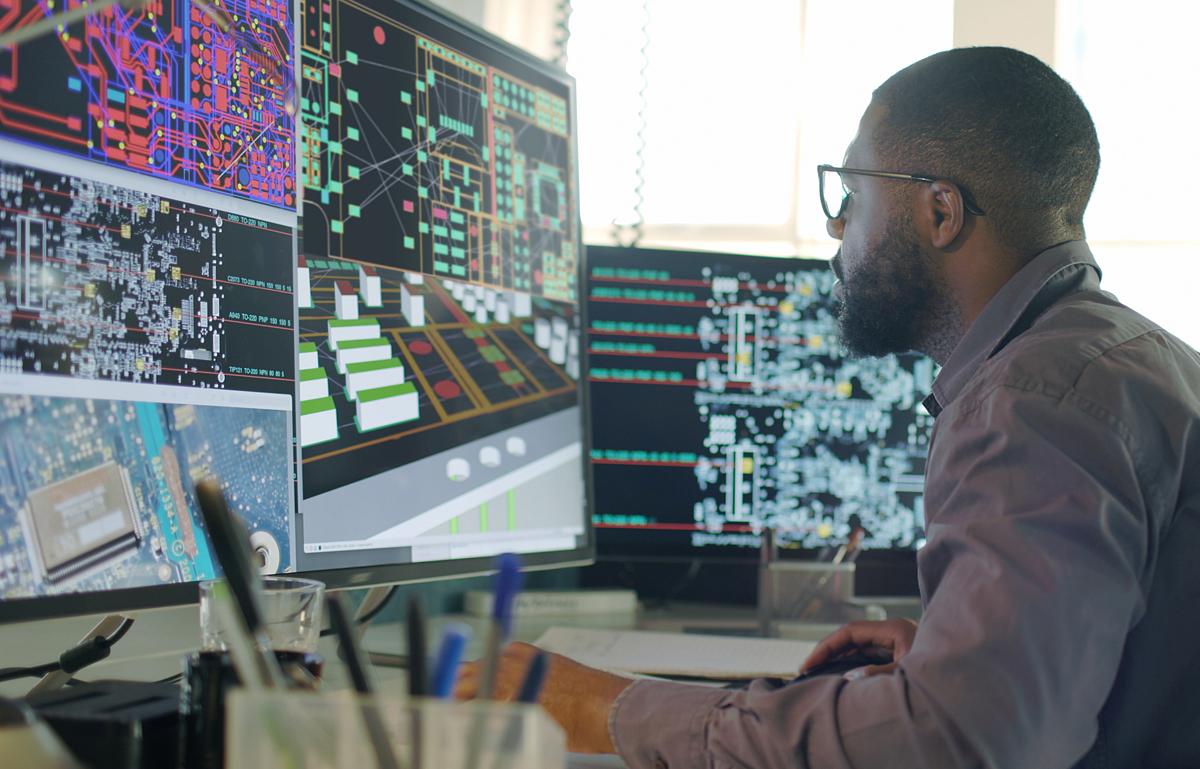
Manufacturing Smarter: How AI Is Eliminating Waste and Fueling Growth
AI Isn’t the Future of Manufacturing. It’s the Present.
Automation revolutionized how manufacturers-built things. AI is revolutionizing how they run the business.
But while enterprise giants pour millions into machine learning, most mid-market manufacturers are stuck at the starting line, unsure what to implement, how to justify the cost, or whether the promised ROI is real.
It is. But only when the business is ready for it.
At Ignite XDS, we’ve helped manufacturing companies shift from gut feel to data-backed execution. Not by bolting on tools, but by aligning operations, marketing, and leadership to a system that’s built to scale. When that foundation is in place, AI accelerates everything.
Faster insight. Smarter allocation. Reduced waste. Greater confidence.
Predictive Beats Reactive, Every Time
In most facilities, equipment doesn’t get fixed until it breaks. Inventory isn’t adjusted until there’s a shortfall. Maintenance is scheduled because the calendar says so—not because the data demands it.
AI changes that. With machine learning layered into the operations layer, manufacturers can detect anomalies, predict failures, and respond proactively. What used to trigger downtime now triggers preemptive fixes. What used to require guesswork now runs on patterns.
One client in the industrial OEM space went from flying blind to forecasting equipment failures six days before they happened. That shift alone extended equipment life, improved workforce efficiency, and reduced lost production time, without adding headcount or hardware.
Predictive AI doesn’t just catch issues. It prevents them from ever becoming issues.
Intelligence at Every Operational Layer
There’s a big difference between automation and operational intelligence. Most manufacturers have some level of automation but very few have end-to-end visibility.
AI bridges that gap. When data is integrated across production, logistics, and customer delivery, manufacturers stop reacting and start optimizing in real time.
In one Ignite engagement, we deployed an AI-enabled dashboard that gave leadership a live view of profitability by customer, delivery route, and sales rep. It wasn’t just eye-opening, it was transformative. Armed with those insights, they restructured territories, cut operational waste, and unlocked over $4 million in annual savings.
That’s the power of operational intelligence: better data, faster decisions, and measurable financial upside.
Forecasting Without Guesswork
Inventory waste isn’t just a supply chain problem, it’s a profitability killer. Overstocked product ties up cash and clogs warehouses. Stockouts delay delivery and damage customer relationships. Most demand planning models are built on old math and gut feel.
AI changes the equation.
By integrating sales trends, seasonality, external market indicators, and customer behavior, AI-driven forecasting adjusts dynamically, down to the SKU level.
One client, previously over-reliant on bloated inventory buffers, now maintains leaner stock with fewer outages. Their demand curve isn’t a lagging indicator, it’s an informed forecast that adjusts daily.
Quality Control That Learns and Adapts
Manual inspections can’t keep up with volume. More importantly, they can’t improve over time. Traditional QC finds problems, it doesn’t prevent them.
With AI-driven quality control, manufacturers move from reaction to evolution. Computer vision systems inspect hundreds of parts per minute, flagging micro-defects invisible to the human eye. But more importantly, they feed that defect data upstream, so processes adjust
before errors escalate.
This is about more than reducing returns or defect rates. It’s about improving your brand reputation, your profit per unit, and your customer confidence. When quality becomes predictive, every unit becomes more profitable.
Workflow Predictability Across the Plant
Efficiency isn’t just a machine setting, it’s a team outcome.
AI-enabled workflow tools now help plant managers do what spreadsheets never could: predict bottlenecks, reallocate resources on the fly, and monitor shift-level productivity with precision.
We’ve seen AI flag daily inefficiencies in production pacing, material usage, and crew deployment, giving leaders the data to optimize before delays become missed deadlines. In industries where margins are thin and timelines are non-negotiable, these micro-adjustments become macro-advantages.
Whether you're running a fabrication line or a field service team, predictability is the edge. AI makes that possible.
Better Data. Better Decisions. Real Executive Impact.
AI isn’t just for engineers. It’s a C-suite asset.
When paired with the right operational framework, AI gives executives visibility into the metrics that matter most: profitability by SKU, margin by customer, true cost per job, and ROI by product line.
In one Ignite client, we uncovered that the company’s largest customers were also its least profitable, draining team bandwidth without delivering bottom-line value. AI surfaced the pattern. Strategy changed the course. Revenue went up. CAC went down.
This isn’t a reporting tool. It’s a business intelligence engine that supports faster, smarter, more confident decisions, daily.
The Bottom Line
AI won’t fix broken systems. But it will expose them.
If your plant runs on outdated processes and disconnected teams, AI will only amplify the chaos. But if you’ve invested in alignment, if your operations, sales, and leadership are pointed in the same direction, AI becomes the multiplier. It gives you speed without compromise, clarity without delay, and insight without digging.
That’s what Ignite helps manufacturing clients build. Not “AI adoption” plans but operational ecosystems where technology supports what drives the business: execution.
See What's Possible: Explore our recent AI Solutions
Ready to Stop Guessing and Start Scaling?
If your manufacturing company is serious about integrating AI the right way, not just automating—but aligning—we can help you build the system that makes it possible.
Let’s talk about what’s holding you back and what’s next.